The state of heavy truck building and manufacturing in general have been beset with serious difficulties and delays that shine a harsh light on the worldwide supply chain. They are keeping new equipment out of the hands of fleets and owner-drivers who would like to upgrade what they are operating.
Take a look at what truck builders are offering this year.
Yet through all the disruptions and shutdowns, research and development has continued on what many experts say is the powertrain of the future: electric propulsion, either fully or partially. In their quest for cleaner air and to combat climate change, clean-air authorities and many governments across the nation are putting up money to make it happen. Meanwhile, others say that diesel, that reliable but highly refined oil-fueled engine, linked to smooth and efficient self-shifting transmissions, will dominate engine sales for the rest of this decade and still be a factor into the 2040s. Many of the truck models they go in have been updated.
Supply chain crippled
Covid is mostly behind us, but the supply chain remains crippled, and truck builders and their suppliers are still not back to normal operations. Some progress is reported, but it might take another year, or even into 2024, before things are working like they were before the pandemic. One statistic shows how hobbled North American truck building still is:
“Manufacturers are 75,000 units behind the number of new trucks needed to move freight,” based on economically derived modeling, according to Ken Vieth, president of ACT Research, which monitors developments in the industry. “During the first seven months of 2019, just before Covid, North American Class 8 production averaged 1,469 units per day, which converts to 363,000 annualized. In that same period of 2022, production was 1,193 per day, or 295,000 annualized. That’s 18.7 percent less and gives you an idea of how far down production is.”
Truck order backlogs stretch out by 10 to 24 months, due to shortages of parts and components. It was even worse in late spring, when the manufacturing shortfall was 100,000 units and daily build rates were lower.
“Production shortages are broad based, with semiconductors at the top of the list,” Vieth said, “plus aluminum parts, tires, wiring harnesses, and down the list of semiconductor-related parts, all in tight supply as well. The sanctions on Russia are squeezing supplies from there—palladium, nickel, steel, and of course oil. You’ll have one part one week, but you won’t have it the next week. Labor, global trade relations, and demographics are issues. The labor force has grown only 2.6 percent, and that affects wages. The Mexican steel industry went down in mid-2021, India steel toward the end of ’21.
“The global supply chain is very fragile.”
Used trucks are similarly impacted, but shortages are declining, said Don Acke, VP of commercial vehicles at FTR Associates, a marketing research firm.
“There’s not significantly more trucks available, but the demand for used trucks [among freight haulers] has gone down,” he said. “Fewer owner-operators are getting into the market. In fact, owner-operators are getting out of the market and going to work for the fleets. In new trucks, construction trucks are pretty much stuck in a holding pattern. Sales have not gone up much, but that’s because the supply has been constricted. They’re not expecting the supply chain to improve until late 2023 or even into 2024. But then the economy will start to slow because of the interest rate hikes. You have pent up demand that will support you for a while. If there’s a recession in 2023, that will make it possible to get trucks, but whether the buyers can put them to good use is another question.”
Dealers are acutely aware of the supply and truck shortages.
“It’s still pretty bad, with everyone kind of bracing for a possible recession,” said Neil Fyda, manager of development at Fyda Freightliner, headquartered in Columbus, Ohio. “Manufacturing costs have gone up dramatically. Last year, we had about a third of the trucks we were looking to get. This year it’s a little more. We’re now trying to figure out how to divide up the trucks we’re getting among customers who didn’t get enough last year.
“The wait time for new construction trucks is two years,” he said. “The factories could build twice as much, but it’s the suppliers. Everything allocated to us has been spoken for. We’re in our third or fourth year on allocation. We have gone on allocation for a single year before, but this is new territory. We have not seen anything like this.”
Used truck supplies are not as short as earlier this year, and they will remain important to dealers and customers into 2023, said Fyda.
Gradual improvements might be noted going into next year, analysts say. The principal culprit is the shortage of all-important microchips that populate the electrical systems of modern heavy trucks and other automotive products. A typical Class 8 truck has 35 to 45 chips, Acke said.
“Demand for chips is extremely strong, and companies that make the machines that make the chips are having trouble keeping up with demand,” Vieth said. But relief is coming: Several chip plants in the U.S. are being expanded to lessen America’s dependance on foreign sources.
Developments in electric trucks
The industry is abuzz with reports of progress in electric-powered trucks. All major North American builders—Freightliner, Peterbilt, Kenworth, and International—are working on them, with most for freight carriage. Others have begun producing e-trucks: a heavy trash-collection chassis from Mack and freight-hauling trucks and tractors from Volvo. Cummins has a division concerned with fuel cells and electric propulsion, and numerous startup companies are in the game. Heavy battery-electric and fuel cell-electric trucks and tractors are hustling freight, drayage tractors are pulling containers out of ocean ports, and light- and medium-duty vans are delivering goods for major package carriers. The longer the routes, the more likely it is that “range-extender” electric trucks, using fuel cells or internal combustion engines to make electricity, become more practical. Technically, those are “series” hybrids, but manufacturers do not call them that.
Missing from the portfolios of EVs are heavy construction trucks, such as dumps and concrete mixers. Experts explain that those vehicles are massive to begin with, and adding large and heavy battery packs would cut into payload. Multi-axle chassis present a packaging challenge: Where can the batteries be mounted? Behind the cab, perhaps, but that would add frame length and more weight. Meanwhile, construction work—travel over rough terrain; the banging that punctuates loading of dirt, rocks, gravel, and paving materials; and the spinning of mixer drums—is especially tough on chassis and components. Manufacturers are gaining experience with on-road freight operations to determine what will live in construction service.
Finally, operators of construction trucks tend to be conservative. They prefer to run what’s tried and true, and not take chances with something entirely new. For those reasons, the odds of seeing electric-powered heavy trucks on streets, highways, and job sites are slim, and are likely to remain so for the rest of this decade.
Electric vehicles of the future will be free of the maintenance items found in diesel-powered trucks, but they will demand attention that fleet managers will need to perform, said speakers at a Technology & Maintenance Council session earlier this year. A truck’s large battery pack will be the primary concern, along with its cooling-heating system. It’s likely that those components will need far less work than a liquid-cooled internal combustion engine in a conventional truck, but the high-tech devices will be new to owners, drivers, and technicians. For instance, battery fires can happen, and flames in lithium-ion batteries are notoriously stubborn.
Cost is also a concern. John Warner, Ph.D., of American Battery Solutions, said costs have come down from more than $1,000 per kilowatt-hour a dozen years ago to about $200 now, but they are still expensive for the hundreds of kilowatt-hours needed to run heavier trucks. Thus electric trucks today still cost half-again or twice as much as equivalent diesel trucks. But that can be offset by government-funded grants, especially in California and other places that are encouraging use of “clean” transportation. Electric trucks now being sold “are going to where the grants are,” said a product manager at one of the manufacturers. And charging infrastructure must be planned, acquired, and installed, all before e-trucks enter a fleet.
Owners will have to keep track of their EV batteries’ state of health, something like they now do for gasoline and diesel engines, said Raul Batista, a fleet manager for Penske Leasing. It will be simpler because there will be no oil changes, valve adjustments, and fuel system work. Technicians and drivers will have to be trained to respect the high voltage within the batteries and in their orange-colored cables, just as anyone who works on today’s hybrid vehicles knows.
Batteries like to operate at about 75 F, and Warner said that most will have liquid cooling systems to try to keep their temperatures close to that mark. EV battery packs need to be heated as well as cooled. According to TKT, an HVAC supplier, a proper heat-management system will include a water/coolant tank, water pump, heat exchanger, compressor, and a condenser coil and fan, all to chill the coolant that encapsulates a battery pack. A heating element warms the liquid coolant in cold weather.
After use in a first vehicle, a battery will be worn, but it can be remanufactured for a subsequent use, something truck manufacturers are already planning for, Warner said. A reman’d battery pack could go into another new vehicle, hopefully at a reduced price compared to all-new, or sold as a replacement in another e-truck. At the end of their useful vehicular lives, they might be repurposed to stationary power for homes and businesses, as a hedge against loss of grid power. Eventually batteries will totally wear out, but instead of being trashed, they’ll be sent to a vendor to be disposed of in a safe manner. For many years, common lead-acid batteries have been responsibly dealt with, and so must it be with high-tech battery packs of the future.
Authorities love electric trucks because of their “zero tailpipe emissions.” But converting to modern diesels is a quicker and less costly way to lower harmful emissions, especially if now-available near-zero-emissions diesels run on renewable biofuels, says a study commissioned by the Diesel Technology Forum, a diesel advocacy group. Adoption of EVs, few of which are currently available, would cost a trucking fleet three times more than converting to today’s new-technology diesels, according to the study by Stillwater Associates. The study looked at air-quality conditions in 10 northeastern states that have adopted California’s regulations for low-emission and zero-emission vehicles.
New-technology diesels are those built since 2007, when diesel particulate filters were adopted, said the Forum’s executive director, Allen Schaeffer. Diesels in 2010 and later added exhaust-gas recirculation. A forum survey showed that 53 percent of trucks now in service have new-tech diesels. Considerable benefits would come from retiring the older trucks, which are common in small construction fleets, and replacing them with the cleaner vehicles.
Cutting particulate matter helps more to improve air quality than NOx reduction, especially in large cities in the Northeast, said Gary Yowell, the Stillwater researcher who did the study. Medical experts say soot harms lungs and leads to numerous health problems. Diesel particulate filters cut soot by about 98 percent, while electric trucks would cut soot by 95 percent when power-plant emissions are factored in, Yowell said. Although solar and wind generation is increasing, many electric-generation plants still use coal, which cannot burn as cleanly as modern diesels.
Low-carbon, renewable bio-based diesel fuels cut emissions even more, he said. They can be used in all diesel vehicles today, so using those in the study area with 100 percent renewable diesel resulted in three times larger cumulative greenhouse-gas reductions by 2032 than the EV scenarios. The results were about the same if B20 were used. The cost of electricity that would run electric trucks is lower now than for diesel, but that is partly because there is no road tax on electricity, Yarnell said. If and when authorities add road taxes, the business case for electric trucks would suffer.
About the Author
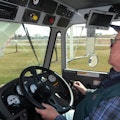
Tom Berg
Tom Berg is widely acknowleged as one of the top truck writers in the industry. He has covered construction for more than 34 years, and has test-driven well over 150 trucks for Construction Equipment.