A Smart Approach to Profitable Equipment Operation
Key Highlights
In this article, you will learn:
-
What the steps are for fleet optimization.
-
How to manage compliance and risk.
-
Logistics and equipment movement.
-
How to maximize value in equipment operation.
-
How to tracking equipment usage.
The Equipment Cycle outlines the four core activities of an equipment-intensive business: acquire and dispose; operate it; repair and maintain it; and continuous improvement. In Part 1, we looked at Acquire & Dispose. Part 2—Operate It—looks at how optimizing a fleet can reduce risk, simplify deployment, boost productivity, and increase utilization.
Simply owning equipment doesn’t guarantee higher profits. Equipment only makes money when it is used and used effectively. Every hour a machine runs either adds costs or creates value. It all depends on how it is used, where it is used, and who is behind the controls. The goal of this stage is simple: Maximize utilization to make the most of every machine, every shift, and every move.
Most businesses understand this and focus heavily on field operations. Value is gained—or lost—where the work happens. Pushing machines too hard—using them beyond their limits or without oversight—leads to more breakdowns, increases fuel burn, and creates safety risks.
The Operate It stage is where planning meets production. It includes four key steps: Compliance & Risk Management, Move It, Use It, and Track It. Let’s break each one down in detail.
Compliance & Risk Management: Manage the risk
This step is about managing risk and staying on the right side of the laws, regulations, and internal policies. Key areas include safety and training, regulatory compliance, and risk response.
The first line of defense is a strong safety culture. Clear expectations for personal protective equipment (PPE), lock-out-tag-out (LOTO) procedures, and toolbox talks create safer job sites. Regular safety meetings and near-miss reporting are opportunities to catch issues before they become incidents. Subcontractors and vendors must be held to the same safety standards. Safety must apply to everyone, no matter who supervises or signs the paycheck.
Staying current with legal and regulatory requirements builds on a strong safety foundation. This includes up-to-date certifications, accurate registrations, and ensuring equipment stays within both registered and manufacturer-rated limits. Insurance should be current, with insurable values listed for each unit. For commercial vehicles, routine inspections and organized driver files help prevent costly violations and delays. When paperwork is in order, equipment is easier to manage.
More fleet optimization
- 5 steps to better benchmarking.
- How to develop a safety culture.
- Utilization is the key metric.
- How to apply the Bradford Factor to equipment downtime.
Good risk management goes beyond the job site: It’s about being ready for the unexpected. Emergency plans for spills or incidents help crews respond quickly and safely. On the business side, using a separate company to hold equipment assets can limit liability and protect the rest of the operation if something goes sideways.
When safety, compliance, and risk plans come together, equipment managers build safer, stronger operations that are ready to perform.
Move It: The right place at the right time
Moving equipment is about the right machine being at the right place at the right time. This step includes planning the move, preparing the equipment, and dispatching it.
Plan for the move. Create an itemized list with accurate weights, dimensions, and insurable values for bills of lading. If values aren’t listed, carriers can default to a standard liability rate, often as low as $0.50 per pound: a 30,000-pound loader bought for $250,000 might only return a payout of $15,000. Make sure all documents—titles, EPA declarations, Certificates of Origin, and registrations—are up to date and easy to access.
Prep the equipment. Use transport brackets or storage stands for loose components and clearly label everything with weights, unit numbers, and tie-down points. If disassembly is needed, include step-by-step instructions with checklists and photos. Don’t forget to label sea containers and attachments with asset IDs and weights to keep the load organized. Take photo packages of the assets’ VIN plates, EPA decals, and GVWR tags. It is much easier to collect this information when the equipment is in your yard than when it’s stuck at a weigh scale or in customs. Include care packages with next-service or filter kits to keep machines ready to run on arrival.
Dispatching puts the plan into action. Schedule transport, confirm load-out lists, and paperwork. Coordinate with drivers and site teams and assign an on-call contact for issues during transit. Clear communication ensures a smooth handoff.
With good planning and preparation, moving equipment can be simple, smooth, and on-time.
Use It: Making money from use of the equipment
It takes more than just turning the key to make money; it requires daily checks, a skilled operator, and staying on top of service.
Daily checks such as pre-use inspections help catch small issues—low fluids, worn tires, broken lights or cracked glass—before they lead to bigger problems. These checks improve safety and reduce downtime. Logging them daily, especially with tablets or mobile apps, builds a clear record of equipment use and condition, supports accountability, and keeps maintenance plans on track. When linked to the work order system, faults can be escalated quickly for supervisor review, which prevents downtime and unsafe operation.
Operator training and competency are key to safe and effective equipment use. Skilled operators understand machine limits—capacity, duty cycle, and attachment use—protecting both people and property. Competency should be tracked, especially for high-risk or specialized gear, with refresher training to find and fix bad habits. Involving operators in daily equipment care builds ownership, pride, and accountability.
Knowing when the next service is due helps avoid missed maintenance and unplanned downtime. Operators should check meter readings, read service stickers, and confirm upcoming service. The best maintenance teams make it easy, placing “next service due” stickers in the cab just like the ones in your pickup truck from the dealership.
Every hour a machine runs either adds cost or creates value. It all depends on how it’s used and who’s behind the controls.
Track It: How much asset life is consumed
Tracking equipment is about knowing where the assets are and how much life is consumed. Success comes down to three things: location, usage, and metrics.
Location means knowing whether each unit is in the yard, on a job site, or in transit. This helps identify what is deployed, what should be available, and how equipment is spread across projects, making planning and identifying underused assets easier.
Usage involves collecting meter readings and billable hours. Meter readings help maintenance teams schedule service and manage replacement cycles. Billable hours show how much time the machine was doing actual work. The difference between them is waste: fuel and machine life burned without return. Reducing this gap boosts profit.
Metrics from every machine should be tracked in one of four states: working, standby, down, or undeployed. These are the building blocks for tracking availability, utilization, and deployment. Together they show what is used, what is ready to use, and what needs attention.
Tracking is more than location. It’s about knowing how much life has been used—and how to make the most out of what’s left. Modern telematics systems can now deliver much of this data in real time.
Optimizing operations is about more than turning the key. Optimization is where the work gets done, money is made, and equipment proves its value. This stage is about working safely, moving machines where and when they’re needed, using them effectively, and tracking how much life was used.
When these steps come together, equipment lasts longer, jobs run smoother, and every machine hour delivers more value. It’s not just about using equipment: It’s about using it with purpose.
In Part 1 of the Equipment Cycle, we look at A Smart Approach to Equipment Acquisitions.
About the Author
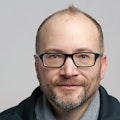
Craig Gramlich, CEM
Craig has extensive experience in equipment management across transportation, heavy lifting, civil projects, mining, and construction sectors. Driven by a passion for cost and data analysis, he excels in enhancing equipment accounting, rate modeling, and developing programs for rate escalation and transfer pricing.
Through Lonewolf Consulting, Craig effectively unites Equipment, Operations, and Accounting departments, leveraging his extensive field experience to help companies streamline operations and find cost savings, significantly boosting ROI.
He holds a Bachelor of Commerce from the University of Alberta and a Certified Equipment Manager (CEM) certification, along with a variety of professional development courses, showcasing his commitment to ongoing professional growth.