Editors note: This article has been updated.
Everything is costing more, and without a doubt, we are spending more and more time on managing cost, fighting inflation, and making sure that every dollar is wisely spent.
But, are we doing the right thing? Do we understand that costs are a symptom of what is going on in the field and that our job is to be proactive and attack the causes of cost? If we are blowing up engines because we are using dirty fuel, then it is no good to cry about the way parts and labor costs are increasing. We must go out there find, the problem and fix it.
The diagram below contains four suggestions to help be proactive in addressing causes of cost.
1) You absolutely have to know and understand the causes of cost. Owning costs are mostly fixed when you ink the deal, so the best thing you can do is to select, purchase, and finance wisely. After that, it is all about making good on the deal and lowering the hourly cost of ownership by extending life and maximizing utilization. These are the two factors that cause your hourly owning cost to be high or low.
The operating cost picture is more complex. The constant categories, such as fuel and wear parts, require that you buy, store, distribute, eliminate waste, and use with care. If the fuel tank is empty and the cutting edge is worn out, you cannot reduce costs by leaving the tank empty or working more hours without changing the cutting edge. The age-related operating cost categories, such as repair parts and labor, are different. You can, through effective inspection and maintenance programs, good operation, and reasonable application, delay the onset of the wear out failures that beset older machines. You can “look after the iron” and reduce both the frequency of breakdowns and the amount you spend on repair parts and labor each time the machine goes down. The frequency and magnitude of spending on repair parts and labor are the two factors that cause your hourly operating cost to be high or low.
2) You must maintain a laser focus on utilization. Low utilization is a root cause and early warning sign of overruns in hourly owning costs. If the fixed costs of ownership come to $6,000 per month, and you have set an owning cost budget of $40 per hour based on 150 hours of utilization per month, then it should not come as a big surprise that you will be over budget by $20 per hour if the machine only works 100 hours.
Stay on top of at least the following four things: (1) Know and understand the two components of utilization: deployment—the number of weeks a machine spends on site—and field utilization—the time the machine works when it is on site. (2) Set good benchmarks for both deployment and field utilization. Expect that the machine will be on site for 40 weeks in the year; expect that the machine will work 35 hours per week when it is on site. (3) Use these benchmarks in your owning cost rate calculation and know that you will not achieve this rate if you do not achieve your utilization benchmarks. (4) Measure and manage both deployment and utilization. Be ruthless when it comes to under-deployed machines. There is no reason to provide a home in your fleet for “in case we need them” machines. There is always the possibility of renting.
For more on equipment asset management, visit
/Institute.
3) Measure and manage reliability. Increasing frequency of down events is a root cause and early warning sign of increases in repair parts and labor cost. Know how often a machine experiences a reported emergency down event (RED event) and disrupts production due to mechanical failure. Each RED event has two impacts. The planning and productivity on the job are impacted, and spending on repair parts and labor increases due to another upward spurt.
There are four things to do to attack the causes of increasing repair parts and labor cost. (1) Train, motivate, and lead your operators. Operators are your first line of defense against RED events. (2) Make sure that your field technicians are knowledgeable and trained on the latest equipment. Make sure that they have the time and resources needed to not only repair the machine but also to eliminate the cause of the original breakdown. You cannot afford to let RED events repeat. (3) Maintain without compromise. Have a good system to observe, measure, and report on the condition of your machines. A worn hose or a cut tire is a warning sign of a pending RED event. Backlog reported problems and complete them before the machine fails and costs go through the roof. (4) Record and report RED events. Measure your ability to be proactive and prevent failures and know that a dollar spent on prevention is worth many, many dollars spent on repair. Believe that it is possible to dramatically reduce the frequency of RED events.
4) Manage fleet age. Machines do not last forever. Keep the average age of your fleet around the sweet spot where the sum of owning and operating cost reaches a minimum. We all know that machines that are beyond their economic life are likely to have high costs and that next year will be more expensive than prior years. You also do not want the average age of your fleet to be too young as this will cause you to experience high depreciation and finance costs and will create a false sense of security in your operating cost budget. It is a delicate balance that requires constant vigilance.
Again, there are four things to do. (1) Establish reasonable expectations for economic life and know where each machine in your fleet is relative to the target lives you have established. (2) Plan ahead. If your benchmark life is 13,000 hours, then it should not come as a big surprise when a 12,000-hour machine becomes a candidate for replacement in two years’ time. (3) Use a well-planned age management and fleet replacement process as a way to constantly resize and reconfigure your fleet. Every replacement is an opportunity to do something new or different and put you in a position to better support change in company requirements. (4) Know that it is possible, and in some cases necessary, to delay replacement, but you cannot deny replacement in the long run. It is hard work and expensive to wind back the clock on an old fleet.
Notice the arrows in our diagram. They all point toward cost to illustrate the fact that utilization, reliability, and age are causes of cost. Proactive management in these areas can prevent problems and minimize the forensic analysis needed to uncover adverse cost trends and attempt to resolve problems of the past. We know that bad utilization causes owning cost per hour to exceed budget; that bad reliability causes repair parts and labor costs to increase; and that old machines have owning and operating costs above the minimum. Use this knowledge, be proactive rather than reactive, and avoid rather than solve problems.
Inflation causes the cost of our parts, labor, and materials to grow. It also causes us to take our eyes off the ball and worry too much about cost. Yes, cost reports are important and, yes, they guide our decisions in complex difficult to see situations. But stay focused on the causes of cost: Get utilization, reliability, and age right; manage them with skill, care, and attention; and then worry about cost.
About the Author
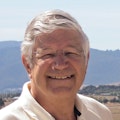
Mike Vorster
Mike Vorster is the David H. Burrows Professor Emeritus of Construction Engineering at Virginia Tech and is the author of “Construction Equipment Economics,” a handbook on the management of construction equipment fleets. Mike serves as a consultant in the area of fleet management and organizational development, and his column has been recognized for editorial excellence by the American Society of Business Publication Editors.
Read Mike’s asset management articles.