What a difference a bigger cab makes. In early 2021, Kenworth introduced “next-generation” midrange conventionals to replace long-running models with comparatively narrow cabs. The new cab is 8 inches wider and better trimmed than the old one, and is based on the 2.1-meter-wide cabin used on the heavy-duty T680 highway tractor and T880 vocational truck. Like the old models, the new trucks are assembled at a plant in St. Therese, Quebec, near Montreal, that is operated by corporate parent Paccar.
They have been accepted “extremely well” by customers, said Erik Kremsner, KW’s medium-duty marketing manager, and the medium-duty trucks are sold out for the rest of the year. A drive in a comfortable and capable T380 service truck demonstrated why.
The steel-reinforced aluminum cab was adapted to smaller medium-duty frames and usually sits relatively low. Not so on our test truck, a 4x4 T380 with a Knapheide body and front-mounted Braden winch; the cab sat high to make room for the four-wheel-drive mechanisms underneath. It was parked at Kenworth’s plant in Chillicothe, Ohio, in a line of new Class 8 Kenworths that were built at this factory.
The T380’s high cab, dark gray paint, and bulky front-end equipment made it look bigger and heavier than it was. I visually compared the cab to those on the heavies; as expected, the cabs were the same size and used the same doors, but—as pointed out by KW test driver Rodney Vanover—they differed in cowl details and dashboard design. The midrange T series’ cabs mate with small hoods that cover their smaller engines, and dashes are simpler and flatter.
Inside, the extra width compared to the old cab was evident and would accommodate a bench seat for two helpers. This one had two air-ride seats with space between to stow personal gear. All controls and switches are close by and easy to use. The centrally mounted 7-inch color screen displays a range of information, such as six virtual gauges that looked like electromechanical instruments that sat in the dash on older-model trucks. Touch a gauge—transmission oil temperature, for example—and it expanded in size as the others disappeared, but they could be recalled with a couple of more touches. In the instrument panel ahead of the steering wheel were a speedometer and tachometer, along with coolant temp and voltmeter, plus a harder-to-see fuel gauge at bottom-center. Headlamps were operated by a circular switch on the dash’s lower left, though I left them off on this sunny day. The four-wheel-drive’s transfer case was operated by a pair of flat toggle-like switches on the dash.
I turned the ignition key and after the electrical system went through a brief self-check, the engine cranked over. I released the air parking brakes and twisted the selector switch on the transmission’s control stalk to D for Drive, then maneuvered my way out of a parking area and onto a nearby surface street. The diesel was a Paccar PX-9, basically a Cummins L9 rated at 300 horsepower and 860 lb.-ft., and the tranny was an 8-speed automated manual, a Paccar TX-8 sourced from ZF, the German gearbox manufacturer that produces it in a plant in South Carolina. I found the accelerator a bit sensitive and had the engine surging and the truck jerking until I braced my foot against the side of the engine cover, then ran things more smoothly.
Now northbound on four-lane, limited-access U.S. 23, the main north-south highway in this region, I pushed the truck to the 60-mph speed limit, then tested its top speed; that was electronically governed at 64 mph. I noticed that some wind noise began at about 55 mph and seemed to come from the large side-view mirrors. The truck rode rather well, considering its hefty leaf-sprung Meritor axles—12,000-pound front and 23,000-pound rear—and modest 192-inch wheelbase. The ride was more like a Class 8 truck’s, I thought. But in leaving the parking area and during subsequent maneuvers, I found a pleasingly tight turning circle, something more like a heavy pickup’s. After a few miles, I spotted a side road angling off to the right; it appeared to be the old grade of Highway 23 that was now a township road. I followed this to a rural intersection with a few buildings and a parking area, and pulled in to snap some photos.
While here, Vanover and I discussed the equipment on the sturdy steel Knapheide service body: numerous cabinets with double-wall doors, one housing controls for a Stellar 12630 crane, others for storage, and another with roll-out tool drawers complete with rubber liners. Perched atop the body’s left-front corner was an Infinity auxiliary power unit that could supply electricity for extended work sessions. We figured that once this truck ended its show and demonstration days, it will be used by a technician to service big yellow earthmoving machines.
Up front was a Braden steel “recovery” bumper that housed a hydraulic-powered winch with a shaft extending to the right through an open-ended tube. Vanover and I wondered what it was for. Later he rummaged through a box in one of the service body’s side cabinets and found a pulley that fit onto the shaft. I joked that it’s meant to spin a belt to drive a threshing machine at antique steam tractor shows. No, said Jim Braden, VP, sales and marketing at Braden Winch in Tulsa, Oklahoma, whom I talked with the next day. That pulley is a “capstan”; wrap a couple of loops of utility line around it, and the capstan will pull the line into place on power poles, for example. Clutches allow the 20,000-pound TR20 winch to be run separately or with the capstan. It’s hydraulically powered by a PTO-driven scroll pump on the transmission, so can run continuously without overheating, which he said can happen with electric winches. That pump also runs the crane. Braden Winch has been owned by Paccar since 1977.
Our ignorance of that information didn’t diminish our driving enjoyment on this springlike mid-winter day, and we continued eastward on State Route 361 that wound through delightful midwestern countryside. Along the way I spotted a dirt trail running south along a cornfield and over a shallow ridge, which provided an opportunity for some off-roading with our 4x4. I turned onto the trail for about a mile into the field, engaging the transfer case along the way. At a circular turnaround, I switched to 4-low and did some 360s. Again, the tight turning radius made the beefy truck nimble, and because of inherent smoothness or that we were on dirt, or both, there was no jerking of the steering wheel or anything suggesting strain in the four-wheel-drive system. Around us were many acres of cut-down corn stalks and I surmised that the trail allows grain-hauling semis to sidle next to combines during the autumn harvest. This trail shows on Google Maps, by the way, and was smooth and dry, thus offering no serious off-road test. We returned to SR 361, which took us to SR 159 and then south to the KW plant.
To sum up: This T380 was a fun conveyance for us and will be a useful tool to its eventual buyer.
About the Author
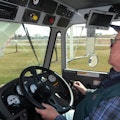
Tom Berg
Tom Berg is widely acknowleged as one of the top truck writers in the industry. He has covered construction for more than 34 years, and has test-driven well over 150 trucks for Construction Equipment.