Golfers know several numbers about their game. These include best score ever, target score on home course, and if they are serious, their handicap. They know these numbers so they can measure improvement and strive to be better. Many golfers will spend a lot of time and money trying to improve these numbers.
Businesses are the same. For construction companies, tracked numbers include gross profit margin, overhead percent of revenue, and months in backlog. Businesses often call these metrics key performance indicators or KPIs.
Contractors that own and operate heavy construction equipment should also track KPIs for their equipment fleets. A company’s bottom line can be significantly influenced up or down by the quality of fleet management. Here are some commonly used KPIs and why they are important.
Actual equipment utilization hours as a percent of planned utilization hours
Many say this is the single most important construction equipment KPI. The investment in construction equipment is significant. It is critical to company profitability that this investment be recovered by performing construction work with the equipment. Utilization hours are defined as the hours a piece or group of equipment operates performing construction work. Cost recovery rates should be based on a planned number of utilization hours per year for each type of equipment. This KPI measures the rate of recovery of the planned hours. If the utilized hours are less than planned, the cost of the equipment for the year is not recovered.
Emergency repairs hours as a percent of planned utilization hours
Emergency repairs are a major contributor to under-utilized equipment. This is where a piece of equipment has been deployed to a project, is planned to be operational, but cannot be used due to some mechanical issue. This not only results in a loss of cost recovery but is frequently disruptive to the job. Fleet managers and company executives should track this closely.
Preventive maintenance hours as a percent of total mechanics hours
Inadequate preventive maintenance is a primary cause of emergency repairs. It is essential that shop management ensure that all scheduled preventive maintenance is performed as required. This KPI tracks whether sufficient time is spent on this.
Total maintenance costs as a percent of total revenue
Total maintenance costs are significant for contractors that operate heavy equipment. Although it is important that all preventive maintenance and emergency repairs be completed, that work needs to be performed in a cost-effective manner to sustain profitability.
This KPI measures the efficiency of equipment maintenance. It is important to note that total revenue used in the calculation should be revenue from performing construction contracts. Revenue from other unrelated activities like quarries or trucking should not be included. The exception to this would be if the construction equipment of these alternative revenues is included in total equipment maintenance. In other words, be careful to compare apples to apples.
Percent of maintenance overtime hours
Overtime hours for mechanics can be a major contributor to inefficient high-cost equipment maintenance. The percent of mechanic time that is overtime hours is a good measure of the efficient use of mechanics. If it is too high, it can indicate poor mechanic scheduling or too few mechanics. Overworked mechanics are not cost effective, because productivity diminishes during overtime hours.
Maintenance costs as a percent of estimated replacement value
There are significant costs to keeping equipment too long. There are three reasons for this. First, older equipment tends to have more unscheduled breakdowns. That leads to job site disruption and unrecovered costs. Second, if a particular piece of equipment becomes known in the organization as unreliable, there is a tendency to deploy it less to job sites. This adds more unrecovered costs. Third, the ongoing maintenance and repair costs of older equipment can grow rapidly. The repair-cost-over-time curve of an older piece of equipment is frequently shaped like a hockey stick.
By tracking annual repair costs as a percent of estimated replacement value, management can determine the best time to dispose of equipment. A rule of thumb is if maintenance is greater than 5 percent of replacement value, it is time for the piece of equipment to go.
KPIs are an alert rather than a solution. These key KPIs can indicate important issues that affect profitability. A good rule of thumb for selecting KPIs is to track those that will lead to management action.
About the Author
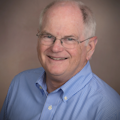
Herb Brownett, CCIFP
Herb Brownett, CCIFP, is the President of Brownett & Associates, LLC, a construction financial management consulting firm in Philadelphia, PA. He has served as CFO, SVP and VP of Finance for a variety of construction companies. Herb is a longtime member of CFMA and was national chairman of both CFMA and the ICCIFP.
Brownett is a construction financial management consultant working with B2W Software.