Everyone agrees that downtime costs money in terms of lost productivity, impacts on other operations, and the cost of returning the machine to work. There is, however, little agreement on how to quantify the impacts and include them in the equipment cost calculation. It is a controversial subject that can easily distract attention from the need to manage hard costs on a day-to-day basis.
Most companies leave downtime cost out of overall equipment costs and focus on the hard, tangible owning and operating costs that are actually experienced. They believe that there are many other intangible costs—such as relative productivity, safety and environmental impacts, and quality of work—that impact the equipment decision, and take the position that the cost of downtime is best included among the intangible costs they talk about but do little about. It is a simple approach: Focus on analyzing the hard costs and include the intangible costs in discussion if you must. This approach certainly works but it does, however cause you to reduce your focus on an important and very real cost of poor maintenance, application and operation.
Other companies attempt to include the cost of downtime in their equipment decision making despite the fact that this is far from an exact science. The nearby diagram provides four approaches. The horizontal axis measures the duration of a down event, and the vertical axis measures the downtime cost expressed in dollars per hour.
Basing downtime cost on the number of down events rather than the duration of down time causes you to focus on reliability as a critical metric.
The green line shows the first, simplest, and most conservative approach. When a machine is down, it cannot work and recover its owning cost and therefore the downtime cost per hour is equal to the owning cost per hour. The cost of downtime is therefore the owning cost per hour multiplied by the duration of the downtime. In our example, the owning cost of the down machine is $25 per hour and the duration of the down event is eight hours; the downtime cost of the down event is $200. Although simple and straightforward, it is very conservative.
The blue line shows the approach when the cost of downtime equals the cost of a replacement machine brought in and used while the original machine is down. Our example shows that a replacement machine costs $100 per hour, so the downtime cost for an eight-hour down event comes to $800. This is not an unreasonable approach with a dozer stripping overburden or a loader stockpiling gravel on its own, and if all that needs to be done is to rent a replacement machine to maintain production while the original machine is down. It is a simple approach that replicates reality under some conditions, but we all know that the impact of downtime is much more severe. It is more than simply replacing one machine with another.
Machines almost invariably work in integrated production teams. This means that a down event in one unit invariably impacts many associated resources, which causes the cost of downtime to be extremely high. When an asphalt paver goes down, for example, a lot of things go wrong and many closely tied associated resources experience significant impact costs. When the single driving resource—in this case, the paver—goes down, it’s the worst situation. If one articulated truck in a spread of four goes down, at least the associated resources can continue at a reduced productivity.
The red line illustrates the worst situation. The cost of the down unit and all its associated resources comes to $350 per hour to give a total downtime cost of $2,800 for the eight-hour down event. The cost of the associated resources can and does vary tremendously, and it is extremely difficult to decide on a number that reflects reality. The red line also assumes that we do not do anything to mitigate the impacts and that the full impact continues for the full period. This assumption is far from reality, as we most definitely do what we can to manage the situation by reassigning associated resources and changing previously laid plans to reduce impact costs.
The black line shows what happens when we take action to manage downtime costs. We did not do anything for the first hour of the down event, but we took action and lowered the cost of associated resources to $250 per hour after three hours. We took more action between hours 4 and 5 and lowered the cost of associated resources to $150 per hour. We acted again in the final hour and lowered the impact costs to the owning cost of the down unit after eight hours. This is what we do in the field. It is, however, absolutely impossible to define, standardize, or even guess at the shape of the black line. There are just too many variables at work.
Our options, then, lie between the simple and doable approach represented by the green line, although it does not reflect reality, and the approach of the black line, which reflects reality but is too complex with too many variables to be doable.
Instead, focus on the simple fact that downtime costs occur because down events occur. Simply put, if we do not have down events, we do not have downtime costs.
Do not worry too much about estimating downtime costs. Reduce or eliminate down events, and thereby reduce or eliminate down time costs. Focusing on down events brings a clear and important focus on reliability: the frequency with which you experience down events. It also brings us to a practical way of quantifying the cost of downtime or, if you like, the cost of lack of reliability. Think about a machine and its primary function, consider the impacts that occur when it goes down, and decide on a well-considered but entirely subjective “penalty” to be applied to the cost of the machine for every down event it experiences.
Yes, it is arbitrary. But so are all the methodologies presented in the diagram. Basing downtime cost on the number of down events rather than the duration of down time causes you to focus on reliability as a critical metric.
Measuring the frequency of down events is easy: You define a work order type code for reported emergency down (or RED) events, and then you simply code and count your work orders appropriately.
Do everything you can to reduce or eliminate reported emergency down events, and you will be doing everything you can to reduce or eliminate the cost of downtime. Focus on the root cause of downtime costs. Eliminat down events.
For more asset management, visit ConstructionEquipment.com/Institute.
About the Author
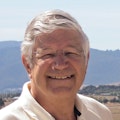
Mike Vorster
Mike Vorster is the David H. Burrows Professor Emeritus of Construction Engineering at Virginia Tech and is the author of “Construction Equipment Economics,” a handbook on the management of construction equipment fleets. Mike serves as a consultant in the area of fleet management and organizational development, and his column has been recognized for editorial excellence by the American Society of Business Publication Editors.
Read Mike’s asset management articles.