Post Pandemic Projections for Asset Management
One of the most disrupting effects of the Covid-19 pandemic—and one that continues to plague the equipment industry—is the shortage of microchips. It has affected equipment availability, cost, and residual value. Accurately forecasting future equipment acquisition budgets will be challenging as new equipment costs and used equipment values will fluctuate with variances in supply and demand. Eventually, new equipment will be available and costs will stabilize. Used equipment will remain scarce, and their values will remain higher than pre-pandemic levels. Many do not expect a return to pre-pandemic market values until late 2023 or beyond.
Prior to the pandemic, there were only minor and sporadic shortages of microchips utilized in the production of new equipment. Class 3-5 light/medium-duty trucks averaged 45 to 80 days, order to delivery, and heavier Class 6-8 trucks averaged between four and six months, each dependent upon class, type, and specialization. Construction and heavy equipment paralleled heavy trucks, running four to six months for delivery of most standard production models. Highly specialized equipment was taking seven to nine months. Equipment availability and cost for both new and used equipment remains stable.
Responses to the pandemic brought an almost immediate economic slowdown, causing organizations to defer acquisition of equipment previously targeted for replacement. Equipment manufacturers responded to the pandemic by reducing production and inventory levels across complete product lines.
While equipment manufacturers were suspending production operations, a global transition in business operations from an interoffice standard to a home office standard quickly emerged. This shift in worldwide business operations caused microchip manufacturers to increase the production of microchips required for home office equipment and the infrastructure required to support the associated increase in internet usage. Production of microchips utilized within the equipment and truck industries was significantly reduced to meet the increased demand for office and communications equipment.
As the world emerges from the pandemic, construction projects have increased and expanded, bringing with it an increased demand for equipment. Microchip production remains targeted toward business equipment and communications. The supply of microchips needed for equipment manufacturing is currently less than half the current worldwide requirement, limiting production and creating a shortage in new equipment availability and escalated used equipment values.
Acquisition costs for new and used equipment have risen significantly in response to the demand. Over the past 18 months, equipment costs have risen more than 10 percent. Escalating inflationary pressures will further increase equipment cost for the foreseeable future. Similarly, used vehicle and equipment values have risen more than 30 percent. The increased demand for used equipment has created limited or no availability and market compression between new equipment cost and used equipment value (see nearby chart). Due to the limited equipment availability, compounded by the microchip shortage and other factors, new and used equipment costs will remain accelerated throughout 2022 and into 2023. This increased cost in the near term is most likely not covered within capex budgets, extending a reduced replacement schedule for many organizations.
Order-to-delivery times have tripled for most vehicles and equipment, with specialized equipment extending sometimes far beyond that of standard production models. Many manufacturers say to expect more than a 12-month wait for such equipment. Some manufacturers have canceled orders or moved them to future-year production schedules. Some have reduced production of specialized or limited-demand equipment, shifting these resources to higher-demand equipment types and models.
Many fleets have extended equipment lifecycles is response to supply shortages (See Construction Equipment’s 2022 Annual Report and Forecast). Others, badly in need of additional equipment, have purchased used equipment. In either scenario, operational costs will increase and reliability will decrease, which will strain already tight budgets and, in some cases, require additional equipment, compounding the issue.
Inventory shortages over the past year in both the new and used equipment markets have created a large backlog of equipment replacement needs. Smaller, sporadic microchip shortages are expected to continue throughout 2022, extending disruptions in balancing the supply and demand of new equipment.
As new equipment becomes available, fleets will begin to replace assets, albeit with increased cost. Even with increased availability, however, it could be well into 2023 before order-to-delivery schedules will recede as a nearly two-year backlog must be filled.
As the backlog subsides, used equipment will become more available, potentially flooding the market and causing used equipment values to plummet, ending the market compression period of equipment value. Anticipated return on investments will remain difficult, and prior residual value projections will be subject to market volatility.
Equipment managers looking to lease and rent equipment may find limited availability there as well.
Interim actions
As the market moves through the next two years, equipment executives should consider the following interim actions for fleet management.
Consider increasing second life machine rebuilds. Total machine rebuilds (see “When Rebuilds Make Sense For Lifecycle Planning” on page 18) can be cost-effective in these circumstances as their cost can range between 25 percent to 50 percent less than a new machine. Reliability and cost savings are dependent upon the depth of the reconditioning applied.
Lifecycle extensions should be re-established to coincide with the level of rebuild applied. Residual values for these extensions should utilize a straight-line approach from pre-pandemic values as the volatility of the current market is overly elevated and most likely will significantly diminish prior to the revised replacement schedule.
An organization-wide utilization analysis will identify underused assets, many of which can be disposed of, after determining anticipated future use and capital-gain implications due to the accelerated used equipment market.
Preventive maintenance programs and schedules must be updated to support new, used, and second life equipment maintenance requirements.
Negotiate with OEM dealers to secure second life rebuild schedules as dealer capabilities will be stressed for these services. Loaner or rental equipment should be included where possible for continuance of operations.
Leasing and rental contracts should be reviewed and updated to ensure equipment availability throughout the period.
Progressive managers will take steps to maintain their fleets cost effectively with sufficient availability for project expansion. Larger fleets have the resources to transcend this period with little interruption, yet smaller ones should move quickly to maintain cost effectiveness and market competitiveness.
Equipment managers must look well into the future and keep a close watch on equipment availability, cost, and value until the market stabilizes.
About the Author
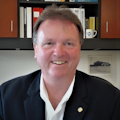
Mike Brennan, CEM
Michael Brennan is a 40-plus-year industry veteran and consultant in vehicle and equipment maintenance management. A three-time recipient of the AEMP Fleet Masters Award, he focuses upon process improvement, facilities management, succession planning, technology, and lifecycle analytics as the cornerstone of success in the equipment management industry.
Read Mike's asset management articles.