Strategies to better manage diesel fuel costs
Diesel fuel powers most construction equipment utilized today due to its high energy equivalent, providing the power for demanding construction work such as digging foundations, trenches, underground drilling, road and bridge construction, power generation, moving aggregates, and much more.
Notwithstanding the advancements over the past decade in engine technology and regulations requiring a transition to alternative fuels, diesel fuel consumed by most trucks and construction equipment will remain the primary energy source for decades to come.
See our Executive Institute for more on asset management.
Fuel is a commodity whose price is sensitive to worldwide supply and demand, making fuel cost an uncontrollable aspect of equipment management. In addition, fluctuations in tax and regulatory measures at all governmental levels along with intermittent production shortfalls make fuel a large fleet expense requiring a high level of diligence to minimize consumption and cost. An effective fuel management, maintenance, and consumption strategy must be an integral part of equipment operations.
An organization’s fuel strategy is dependent upon the size, capability, and geographic service area of the organization. Having a proactive fuel management strategy will increase the reliable performance of equipment and prevent unexpected failures caused by fuel contaminants.
Equipment managers must have a variety of methods available to adequately supply fuel to their fleets, have the ability to refuel in a variety of geographical areas at any time of the day or night, and effectively coordinate fuel deliveries with on-site project managers. Communication with fuel suppliers and across all functions within the organization utilizing and fueling equipment is imperative to accomplish this task.
Three distinct fuel supply management options make fuel management a complex and detail-oriented function of the equipment team.
- Organizations operating construction equipment and associated vehicles commonly outsource on-site fuel supply to vendors within a project’s specific regional area, regardless of fleet size.
- Regional and localized organizations commonly have fuel storage and dispensing operations at their regional maintenance/storage yards, as well, and transport fuel to project sites as needed.
- Many complement these strategies through deployment of fuel card systems for on-road trucks and support vehicles.
Automate fuel management
To manage a comprehensive fueling strategy, equipment managers must incorporate an automated fuel-management system into their equipment management software system. The fuel-management system should monitor and track all fuel delivery, dispensing, and expense transactions of the fleet. These systems deliver a high level of fuel data and consumption detail per asset and decrease the possibility of fuel misappropriation through the automated dispensing management.
In addition, an integrated electronic tank management or SCADA system effectively monitors and manages on-site inventory levels and, most importantly, fuel deliveries at all tank locations over large geographical service areas. All storage tanks should have established minimum/maximum fuel levels with an incorporated re-order volume allowing the system to automatically notify the equipment team of the need to order fuel. Establishment of such values and process ensures that adequate fuel is available without workflow interruption.
Fueling card transactions must be electronically imported daily into the management system by specific asset to capture comprehensive fuel consumption and cost.
Maintain fueling infrastructure
The most important aspect of fueling operations is cleanliness of the fuel. High-pressure fuel systems within modern equipment will not tolerate dirty or contaminated fuel. Injection, aftertreatment, and onboard filtration systems are vulnerable to failure caused by poor quality, dirty, or contaminated fuel. Failure of these components cause unscheduled maintenance and machine downtime.
Poor or contaminated fuel can come from many sources: unfiltered fuel deliveries, moisture through tank vents, tank-to-tank transfer of contaminated fuel, cross fuel type contamination, faulty equipment, and others.
To defend against fuel contamination:
- Tank vents should be equipped with a desiccant type, 1-micron moisture filter to reduce moisture entry.
- Storage tanks should be regularly tested for water and other contaminants. A proactive process is to extract approximately 1 percent of fuel from the bottom of each tank semi-annually to remove any water and settling contaminants.
- All fuel deliveries should be filtered at delivery, and all fuel dispensers must be filtered at the point of delivery to a minimum of 2 microns.
- All tanks must be clearly identified by the product to avoid cross-contamination of fuel.
- Minimize tank-to-tank bulk transfers.
- Fueling equipment and infrastructure should be maintained to exacting standards to reduce potential contamination due to failure.
Saddle tanks mounted in service and support vehicles are a common source of contaminates, as well. Often, these tanks lack vent filtration or sufficient filtration in the dispensing stream, passing contaminants directly into onboard fuel tanks. Saddle tanks should be filtered at a 2-micron level in the dispensing equipment.
Small, handheld portable fuel tanks/cans should be avoided. Such cans are often left in the back of support trucks, open to the elements, and poorly labeled. This increases the potential for water, algae/microbe, and cross fuel contamination.
Some organizations have detailed fuel-management programs, recording consumption at the asset level, but others estimate fuel consumption and cost per machine using a standardized formula. Others record fuel use and consumption by the project, site, or function within a project’s specific budget reconciliation without asset consumption detail.
Per-asset consumption detail is imperative to effectively manage fuel consumption and associated cost. It is the underlying variable in fuel cost that can be controlled by the equipment team. There are many ways to manage reductions in fuel consumption. Here are some that yield better results.
- Electronically manage the fuel program with automated asset identification. Per-asset detailed data allows for exception monitoring of assets consuming fuel at a level higher than average, which may indicate maintenance needs or misappropriation of fuel.
- Prioritize preventive maintenance and repair to keep equipment at peak performing levels. Well-maintained assets achieve the highest levels of fuel efficiency.
- Institute and enforce an anti-idling policy. An idling engine achieves zero productivity per hour while consuming potentially a gallon or more of fuel in the same time span. Operator training and leadership enforcement of the policy are key within this initiative to achieve the best results.
- Right-size/type assets for the specific work. Correct size and type equipment allows for increased operational efficiency and reduced effort.
- Train operators regularly to increase efficiency. Highly trained operations offer the greatest job site efficiency and reduce fuel consumption.
- Maintain proper tire inflation. Underinflated tires cause a significant increase in fuel consumption.
As fuel cost continue to rise, implementation of an effective fuel management, maintenance, and consumption strategy should be a primary objective of the equipment team. Utilization of modern technologies introduced should be intensely researched and implemented as needed to better manage this liquid gold, guarantee cleanliness and high quality fuel, and reduce consumption and cost.
About the Author
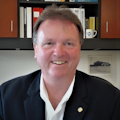
Mike Brennan, CEM
Michael Brennan is a 40-plus-year industry veteran and consultant in vehicle and equipment maintenance management. A three-time recipient of the AEMP Fleet Masters Award, he focuses upon process improvement, facilities management, succession planning, technology, and lifecycle analytics as the cornerstone of success in the equipment management industry.
Read Mike's asset management articles.