More on skid steers
- Top skid steers less than 2,000 ROC.
- Best practices for trailering compact equipment.
- Machine control systems can save time and money when deployed on smaller machines.
- Uptime tips for skid steer loaders.
- Skid steer prototype arrives at National Inventors Hall of Fame.
In this article, you will learn:
- The benefits of a small skid steer loader.
- The cost of owning a small skid steer loader.
- What technology is available on a small skid steer loader.
- What attachments work with a small skid steer loader.
The skid steer market has been caught up in a bigger-is-better frenzy for some time. In the midst of the move to 100+ horsepower machines, is there still a place for the smallest models? Absolutely.
Skid steer loaders of up 2,200 pounds rated operating capacity (ROC) at 50% tipping load offer distinct advantages over other compact equipment. They’re more capable than mini loaders—racked or wheeled, stand-on, or pedestrian. They’re faster than compact track loaders and have lower costs, both initial acquisition and owning & operating. They’re more maneuverable than compact wheel loaders and usually offer more auxiliary hydraulic performance.
To borrow a term from the world of computers, small SSLs have a smaller form factor than many other machines. This enables them to access smaller job sites, including through doors and gates to operate in interior spaces.
Size also matters when trailering. Smaller machines fit on smaller trailers, but skid steers are often transported with an array of attachments. These may all fit on a trailer, but they must be arranged in adherence with the 60/40 rule where 60% of the weight is ahead of the trailer axles. Violating this rule can lead to sketchy handling, including fishtailing. The small form factor of a small skid steer provides much more flexibility in load placement, especially when there are other items on the trailer or when the trailer is comparatively short.
Weight is also a factor in trailer selection and whether a CDL is required for transport. Bridge load limits, especially in the Northeast, also must be considered when trailering larger, heavier machines.
What technology is available for small skid steer loaders?
Technology tends to appear first on larger, higher-cost machines where the add-on expense of new tech is more easily absorbed. Once research and development costs are recovered, this tech tends to trickle down to smaller equipment on a lower cost-per-unit basis. There are also economies of scale—more installations on more machines lowers the cost of each inclusion—and economies of scope—adding similar tech to SSLs and CTLs results in lower cost per installation than adding it to just one of those categories.
Technology has come to small skid steer loaders…sort of. Sometimes the technology is a lesser version of similar tech on larger, more expensive machines. A Telematics Lite with engine and operating data but not geofencing or remote updating would be an example. Telematics on small skid steers range from none to reduced feature to full feature versions.
Sometimes the technology is optional. Buyers of small skid steers can be price-sensitive, and technology always adds cost. Rental houses often skip the tech to enhance their ROI on equipment purchases. Owner-operators become fluent in the operation of their machines, and operator-assist features may have little perceived value to them. Features such as comfort ride and self-levelling, therefore, may not be standard. The same with creep mode and work tool positioning. These may be offered à la carte or only as part of a package or not offered at all. Some features, such as 2-speed drive, are factory-only options. Some can be installed by the dealer. Some are available from third parties for installation by those entities or by the equipment owner.
Choosing the right model of small skid steer entails the same process as with any equipment: Define the applications, decide which tools and attachments are required by those applications, then match the attachment(s) to the correct machine. It’s just a little trickier here at the small end of the skid steer market where there are so many variables to consider.
How much does a skid steer loader cost?
Small skid steers are relatively low-cost machines that are also notoriously rugged, capable of continued operation despite chronic neglect. Going back to the world of computers, customers can calculate MTTF, or mean time to failure. Know how long a skid steer with zero maintenance and repair will typically last, sell it at 95% of those hours, buy another and repeat the process. That is certainly one way to minimize O&O costs, but not one recommended by any OEM or asset manager.
At a minimum, OEMs recommend adherence to the maintenance protocols provided with the machine. These include daily checks, greasing at prescribed intervals, and adherence to PM intervals, including the Severe Service schedule when applicable.
Beyond that, regular fluid sampling is a cost-effective way to anticipate repairs and take necessary pre-emptive steps. Spec’ing the machine properly is a key in managing O&O costs, including choosing the right tires. Operators should alternate direction of counterrotation steering, as they would alternate turning direction with undercarriage equipment. Maximizing the use of telematics can help minimize costs.
Dealer service agreements and extended warranties can offer excellent value. They can often be bundled into the original purchase so the cost is part of the monthly payment. When these arrangements are transferable, they contribute to the residual value of the machine.
Although it can be less true for small skid steers than for large equipment used in production applications, downtime is the main cost. In the extreme case of MTTF, a miscalculation resulting in failure and downtime quickly erases any gains made by skipping maintenance. But even where some maintenance is performed, cutting corners can lead to downtime. Small skid steers are low-cost machines. Maintaining them is a low-cost proposition. Downtime is rarely low-cost.
What attachments are available for small skid steer loaders?
Big skid steers and big attachments have shared a development curve, yet growth in smaller attachments has outpaced that of their bigger versions. And it’s not just buckets, forks, and grapples. Attachment design is scalable, and there are smaller versions of virtually any attachment that are suitable for use with these smallest skid steers. That includes attachments once thought too resource-hungry to be run by smaller equipment, things like mulchers, cold planers, and rock saws.
It helps that small skid steers have upped their auxiliary hydraulics. Those aux systems still vary widely by brand and model, but it’s not uncommon to find skid steers in this ROC category with 25 gpm and 3,000 to 3,500 psi; some even have high-flow options with gpm in the low- to mid-30s. Fleets whose businesses focus on high-volume work with high-demand attachments are likely served better by larger machines, but managers with these smaller skid steers are not excluded from adding these applications to their portfolio of offerings.
One issue remains, however: weight. Small skid steers with sufficient auxiliary flow and pressure may still lack the weight to handle some attachments. And it’s not just the weight of the attachment but the placement of that weight, which may be far in front of the skid steer. Add-on suitcase counterweights can help, but not a lot.
Some technology is sufficiently evolved to pair with smart attachments, where the attachment and host machine recognize each other and play well together. Joystick controls convert to the pattern suited to run the attachment. Hydraulic performance is tailored to the needs of attachment. Creep mode or operator assist functions are automatically deployed.
Small skid steer OEMs remain aware that these machines often go to customers who are price sensitive. That will inhibit development. But at some point, the tech and features become cost-effective for one or a few OEMs and their list of standard features expands. Because of the psychology of hedonic adaptation, customers will quickly assume that tech and features once considered appealing but hardly necessary will become the expected baseline. Remaining OEMs will scramble to catch up.
These advances will include more tech, more electronics, more operator-assist functions. But they will also include what are now labeled “alternative fuels” such as hybrids and battery-electric vehicles (BEV), as well as hydrogen, whether as fuel for internal combustion or as a hydrogen fuel cell.
About the Author
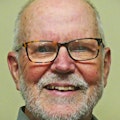
Richard Ries
Richard Ries began his free lance journalism career in June, 1985, calling on his experience as a service manager at a Honda motorcycle dealership to place his first article. When the motorcycle market collapsed in the late 1980s, he moved to the booming bicycle market. Finding that market lacked the professionalism he sought, he moved to construction in 1995 and has remained there ever since.
His countless clients have included entities in Australia, England, France, Germany and Scotland. He has written for trade and consumer periodicals, equipment and component manufacturers, government agencies and non-governmental organizations. Clients have also commissioned him for photography and videography work, either stand-alone or as part of package of text and images.