Sponsored Blog
In our last blog, we outlined a few of the benefits of connecting the technology on your job sites to further increase productivity and profitability. One great example of connected site technology on a huge scale is a project called CoalConnect.
Billed as the largest machine control earthmoving project in the southern hemisphere, the CoalConnect alliance used a connected site strategy to integrate advanced survey, construction and earthmoving technology for a site with a footprint that was 167 km (103 miles) long.
As its name implies, the Queensland AU project was designed to construct a new rail line and connect with two existing rail lines in order to move coal from mines to processing much more efficiently.
Naturally, on a project of this scale, there were many challenges:
• The relatively flat land is located in four flood plains, this project required extensive drainage systems and culverts to manage water flow
• In addition to the new rail project, the existing rail lines were to be upgraded and 15 level crossings, six road intersections, 11 railway bridges, and two road-over-rail bridges were to be constructed
• The scale also meant that crews spread out across the project would need to have stable, consistent positioning data at all places and times.
By committing to the use of connected construction technology site-wide, and planning for these challenges up front, productivity took on a scale matching the project’s size. The CoalConnect team built a coordinate framework across the entire site and established a network for GPS base station correction. Over 42 pieces of machinery were equipped with 3D grade control technology... including 20 graders, 16 excavators, five bulldozers, and one compactor.... all connected and sharing data with the main construction office.
In all, the team excavated 3.16 million cubic meters of bulk of earthworks across three sites, which was done in more than 150,000 truckloads over the two-year construction timeframe.
The use of connected construction technology resulted in many, many areas of productivity improvement. Remarkably, despite setbacks and severe weather events, including two cyclones and extensive flooding, the project as a whole was completed on time. And some of the most impressive savings was in the area of site positioning.
A typical rail project of this scale and construction timing would require an army of survey professionals to be working onsite. This would add significant personnel, equipment, and travel costs, not to mention cumbersome logistical and data integrity issues. Instead, only a handful of surveyors and grade checkers were required; in all, a savings of hundreds of thousands of man-hours.
How’s that for big savings?
You can read the whole story about the CoalConnect project here. Or you can search for and read stories about why and how customers made the decision to implement technology, and what their experience has been, at trimble-productivity.com.
About the Author
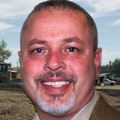
Lamar Hester
Lamar has been with Trimble for 15 years and is currently Sales Engineers Manager for the Americas region for Trimble’s Heavy Civil Construction Division of Trimble. Lamar has extensive field experience in civil construction, site positioning technologies, 3D machine control, and 3D data preparation & modeling.
Lamar Hester has a B.S. from Auburn University, and a Masters in Information Technology from American Intercontinental University.